Servo drive CMMT-AS/CMMT-ST & servo motor EMMT-AS
Complete drive system, consisting of servo drive and servo motor, with seamless connectivity in hardware and software.
Servo drive CMMT-AS and servo motor EMMT-AS are connected via a one-cable solution and can be put into operation very quickly and easily using the Festo Automation Suite. Servo drive CMMT-ST for low voltages from 24…48 V DC and 150…300 W continuous power – extremely efficient moving and positioning.
- For point-to-point and interpolating motion with focus on dynamic motion and precise positioning
- Complete integration into other third-party control concepts or directly on the control system CPX-E from Festo
- Have your drive system up and running in only 5 steps with the initial commissioning wizard
- Compact and optimised package design as well as clever 2-sided operating and connection concept ensure low space requirements in the control cabinet
The servo drive CMMT-AS at a glance
As a state-of-the-art compact servo drive, the CMMT-AS is an integral component of the Festo automation platform. It is designed for dynamic motion, point-to-point and interpolating, in demanding applications in packaging machines, in assembly and handling technology or in the electronics industry.
The direct fieldbus integration to all important controller manufacturers enables the direct integration of the CMMT-AS into all application programs simply and efficiently.
- Servo drive with Ethernet-based and simple integration into automation solutions with controllers from e.g. Siemens, Rockwell, Beckhoff and others
- Control element CDSB with touchscreen and USB interface for full-text diagnostics or for simple data backup on site and for transferring the same program data to several CMMT-AS, e.g. for series machines
- Two multi-encoder inputs: one for connected motors and a second for e.g. a redundant measuring system in safety-related 2-channel solutions
- Auto tuning function supports easy commissioning of rotary and linear motions and automatically optimises the control behaviour of connected servo motors and linear mechanisms from Festo – also support commissioning with third-party mechanical systems
- Connection of the servo motor EMMT-AS via single-cable solution (OCP) for current and encoder and brake simplifies and significantly reduces the installation effort and saves space in the control cabinet
- Safety functions integrated as standard, e.g. safe torque off (STO), safe stop 1 (SS1), safe brake control (SBC)
The servo drive CMMT-ST at a glance
The ultra-compact low-voltage controller CMMT-ST represents excellent economic efficiency and maximum space efficiency. Positioning tasks or movements with low continuous power requirements of up to 300 W can be solved virtually perfectly with the CMMT-ST.
Its small dimensions enable optimum use of the installation space in the control cabinet. When operating the CMMT-ST on the existing 24 V DC network and with a maximum continuous output of 150 W, it is even possible to do away with the extra power supply unit. This again saves costs, reduces the installation effort and lowers the required cooling capacity.
- Ethernet-based servo drive that is easy to integrate into Festo control solutions or automation solutions with controllers from e.g. Siemens, Rockwell, Beckhoff and others
- The auto-tuning function makes commissioning of rotary and linear motions really easy and automatically optimises the control behaviour of connected servo motors and linear mechanisms from Festo. It also supports commissioning with third-party mechanical systems
- Integrated web server for quick and easy online diagnostics, as well as the transfer and update of firmware and parameters.
- Integrated safety functions as a standard: STO safe torque off and SS1 safe stop 1
The servo motor EMMT-AS at a glance
The EMMT-AS is an AC synchronous servo motor for demanding and dynamic applications. Its space-saving single-cable solution reduces installation effort and time, improves the clarity of the system and simplifies maintenance.
Technically, it is characterised by an extremely low detent torque, which ensures very good controllability and thus path accuracy during positioning tasks, whether linear or rotary. The integrated electronic nameplate on which all relevant motor data is stored and can be read out directly by the CMMT-AS, makes commissioning easier, safer and, above all, faster.
Selected technical features:
- 3 sizes 60/80/100 with up to 7.6 Nm nominal torque
- Single-turn or multi-turn absolute encoder
- Optional holding brake
- Degree of protection: IP67 for housing and plug connected, IP65 on the shaft with optional sealing ring
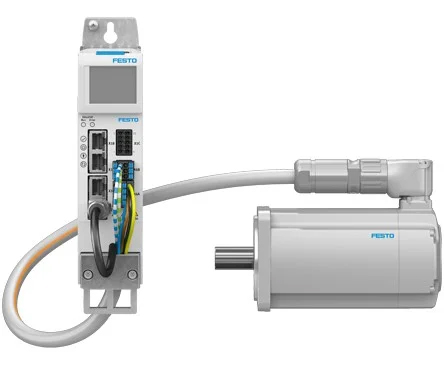