More Efficient, More Flexible, More Productive – The Future of Your Production
The Motion Terminal VTEM is the first standardized platform on the market worldwide whose valves are controlled by Motion Apps. What do such digitized pneumatics mean for you as an OEM or end user? You benefit from simpler engineering and ordering, faster system setup and installation, and more efficient and flexible operation – thanks to the intelligence of the integrated sensor technology, for example. With VTEM, you get your system in the field of pneumatics fit for Industry 4.0 when it comes to motion, pressure, and flow control.
How Can You Benefit from the Motion Terminal VTEM?
Reduce Complexity through Digitalization
- Simplified engineering, simplified system setup, simplified operation – with their wide array of functions, the Motion Apps replace up to 50 individual functional components and thus simplify design. This reduces the number of part numbers required and the system needs less installation space.
- The built-in intelligent sensor technology for control, diagnostics, and self-learning tasks eliminates the need for additional components and having to integrate them into the system.
- Copy and paste: once the parameters have been defined, you can simply apply them to other systems. The time-consuming process of manually setting up and fine-tuning your systems is now a thing of the past – all your actuators are synchronized perfectly.
- Accidental manipulations are impossible.
Leverage Adaptability for Greater Productivity
- Significantly minimize your setup times: set parameters once, access them again and again. Presets eliminate the time-consuming process of manually setting new parameters when changing formats.
- You achieve maximum process stability because the Motion Apps always preset exactly the same parameters. In the event of deviations, the self-regulating apps independently adapt to changes in parameters.
- Reduce cycle times by up to 70%, for example, with the “Soft Stop” Motion App. Smooth retraction into the end position almost completely prevents wear-intensive vibrations, e.g. in the case of tool changer doors.
- Cut energy consumption by up to 40% and still increase the dynamic response of the cylinders by up to 30% through the intelligent use of compressed air, e.g. by selecting the right set of parameters for each product and defining a lower pressure for the return stroke.
- Overall, you can perfectly model movements through the highly customizable interaction of pressure and flow and also vary the traversing speed, even within a single working stroke – such as when switching from speed to maximum force during the press-fit process.
Access Your Process Data at Any Time
- Improve overall equipment effectiveness (OEE) by making decisions based on historical or current data.
- Integrate predictive maintenance into your diagnostic concept – you can analyze the process data provided by the built-in sensor technology. This ensures that your maintenance is based on actual requirements and that you can plan your maintenance cycles in a more systematic manner.
- With the “Leakage Diagnostics” Motion App, you can check your application regularly and detect any leaks early on, saving energy and cutting costs.
- Gain confidence through traceability: by digitally monitoring all key process parameters, convenient traceability is now possible for the first time – without the need for additional components.
- Optimize your system using the testing features. Via the web server, you can use WebConfig independently of a higher-level controller to check every movement in advance and identify the performance limits of your system.
- Interface standards for Industry 4.0 thanks to OPC-UA via the CPX automation platform.
Greater Communication – the Key to Your Future Success
The Motion Terminal’s enhanced decentralized communication increases the possibilities offered by pneumatics. At the same time, it becomes much easier to implement functionality that previously required complex designs and time-consuming adjustments. You can create highly sophisticated movements, including new sequences. In addition, it uses this communication to monitor essential parameters such as travel time, pressure and flow rate, and corrects itself if necessary. The intelligence of the Motion Apps unlocks numerous options, e.g. to control and analyze interconnected processes – even in networks.
App-Based Functionality, Built-in Intelligence
Functions are implemented in the Motion Terminal through Motion Apps and built-in, flexible, and programmable processors. This built-in intelligence gives the system significantly greater flexibility compared to hard-wired hardware. You can now make modifications locally within the system. They require much less bandwidth for communication and at the same time reduce the complexity of controlling and programming the entire system.
Functions and Hardware Decoupled
The Motion Terminal is equipped with powerful processors. This decentralized intelligence in the built-in controller [1] and the Motion Apps [2] decouple pneumatically required functions from the mechanical hardware for the first time. You can easily assign them via Motion Apps and you only need one valve type for a wide variety of pneumatic movements.
Built-in Sensor Technology for a New Level of Flexibility
Built-in sensor technology makes the valves in the Motion Terminal intelligent. The newfound flexibility enables cylinders, for example, to perform new tasks. Movements can be modeled on a highly customized basis and adapted to the task at hand extremely efficiently. This significantly improves the performance of your production operations and typically cuts costs – even when you retrofit systems.
The smart actuator technology in the Motion Terminal is made possible by a bridge circuit consisting of four proportionally controllable 2/2-way valves with built-in sensors. Piezo pilot and diaphragm poppet valves create the key conditions necessary for independent pressurization and exhaust. This allows you to implement a wide variety of common valve functions in a single valve – even proportional pressure control or complex control solutions such as Soft Stop.
Comparison of Reference and Actual Values for Self-Adjusting Parameters
In an adaptive, intelligent, flexible system, permanently embedded sensors are absolutely essential – whether they are used to adapt to changes in environmental conditions, to system parameters such as fluctuations in supply pressure, or to gather all the necessary information for big data processes.
The combination of built-in sensors [3] and the software-based, flexible adjustment of pressure and flow enables the system to carry out evaluations and adjustments on its own. This not only cuts costs, it also simplifies the entire system from conception to modernization. This means, for example, that external load cells are no longer needed for condition monitoring during pressing procedures. Or you can reduce the cycle time by flexibly configuring the process parameters, even within a single stroke. This often means that you can then use smaller cylinders.
For certain tasks, data from external sensors can be processed in real time via separately integrated inputs [4] for internal control purposes. You can use this to develop optimized pneumatics applications.
Incidentally, you can also use it to cost-effectively add intelligence and transparency when modernizing your tried-and-tested, existing systems – then retrofitting really pays off.
Easy to Configure via the User Interfaces
With the Motion Terminal, you have several communication channels with user interfaces at your disposal at the same time. You can make adjustments quickly and easily – directly via Ethernet, via web browser, via the intuitive WebConfig interface, or via a conventional machine controller’s process data. The ability to easily configure functions via our Motion Apps speeds up system setup, reconfiguration, and system modifications. You can extract data via a transfer channel.
Ready For Tomorrow: the Communication Interfaces
Open, global communication interfaces ensure that the Motion Terminal is prepared for future developments such as software services and global networking. With the OPC-UA interface on the CPX-CEC, you can create a platform and vendor-agnostic, service-oriented architecture – the ideal conditions for Industry 4.0.
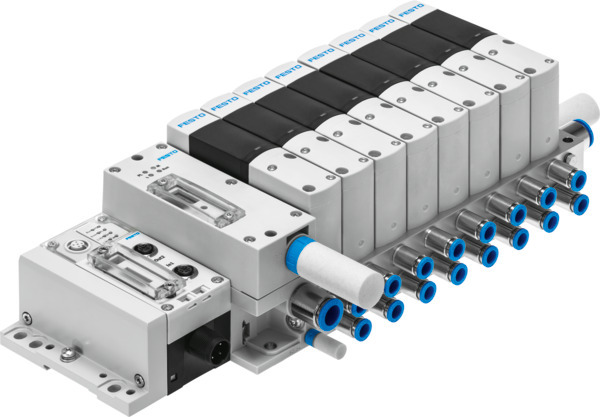